High performance MEMS inertial sensors
Tronics is the only provider of high performance MEMS inertial sensors to offer both closed-loop accelerometers and gyros with digital interface and SMD package. Our tactical-grade digital acceleration and angular rate sensors exhibit a compact form-factor and low power consumption to provide a low SWaP-C alternative to analog quartz accelerometers and Fiber Optic Gyros (FOG).
Closed-loop digital MEMS inertial sensors
Through our closed-loop, digital and SMD sensor architecture we have taken high performance MEMS inertial sensors components to an unrivalled level of performance, stability, reliability, and ease of integration. The closed-loop electronics, also called force-rebalance or force-feedback, brings several key advantages to our high performance MEMS inertial sensors, including:
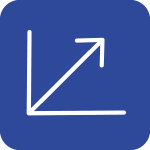
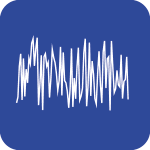

High signal to noise ratio
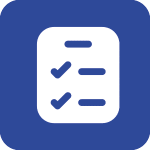
Besides, our digital electronics architecture is fully hard-coded and contains no software. This eases the certification of our high performance MEMS inertial sensors by our customers for safety-critical applications.
Low-SWaP alternative to quartz accelerometers and FOG gyros
We have taken care of every detail to provide our digital acceleration sensors and angular rate sensors with the highest possible level of stability and repeatability under vibrations and fast temperature changes. Consequently, our high performance MEMS inertial sensors exhibit performances that were yet only achieved by bulky, expensive, power-consuming and non SMD solutions such as tactical-grade analog quartz sensors, Dynamically Tuned Gyros (DTG) and Fiber Optic Gyroscopes (FOG).
MEMS sensors for demanding high performance IMU and INS
Our digital MEMS accelerometers and gyros are well suited for system manufacturers requiring high performance MEMS inertial sensors with high precision, high stability and high repeatability under strong vibrations and temperature changes. In addition, the digital SPI interface and hermetic SMD package simplifies the system integration and reduces the bill of material and assembly costs compared to tactical-grade analog solutions.
We therefore enable a swift development, qualification, and production of small, light, and affordable high-performance inertial systems such as:
- Motion control systems and Motion Reference Units (MRU)
- IMU
- INS
- AHRS